
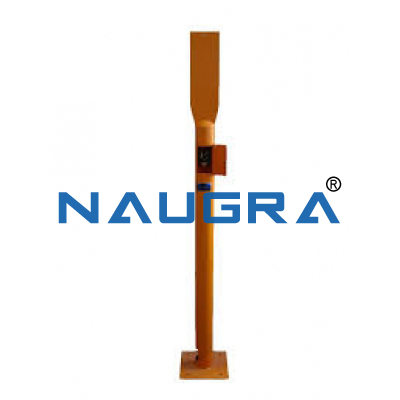
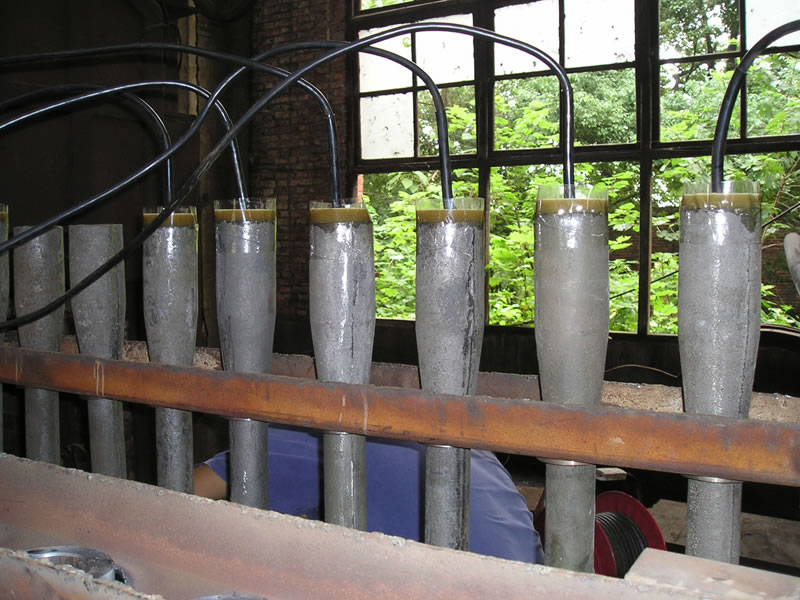
However, in some circumstances - where there is a risk of hydrogen embrittlement, for example - this lower voltage is advantageous, as overprotection is avoided. Zinc has a relatively low driving voltage, which means in higher-resistivity soils or water it may not be able to provide sufficient current. Zinc is considered a reliable material, but is not suitable for use at higher temperatures, as it tends to passivate (the oxide layer formed shields from further oxidation) if this happens, current may cease to flow and the anode stops working. Typical uses are for the hulls of ships and boats, offshore pipelines and production platforms, in salt-water-cooled marine engines, on small boat propellers and rudders, and for the internal surface of storage tanks. Zinc and aluminium are generally used in salt water, where the resistivity is generally lower and magnesium dissolves relatively quickly by reaction with water under hydrogen evolution (self-corrosion). An aluminum-zinc-tin alloy called KA90 is commonly used in marine and water heater applications. Where this is a concern, zinc anodes may be used. Leading to hydrogen embrittlement or to disbonding of the coating. More simply put, this takes advantage of the relatively low stability of magnesium, aluminum or zinc metals they dissolve instead of iron because their bonding is weaker compared to iron, which is bonded strongly via its partially filled d-orbitals.įor this protection to work there must be an electron pathway between the anode and the metal to be protected (e.g., a wire or direct contact) and an ion pathway between both the oxidizing agent (e.g., oxygen and water or moist soil) and the anode, and the oxidizing agent and the metal to be protected, thus forming a closed circuit therefore simply bolting a piece of active metal such as zinc to a less active metal, such as mild steel, in air (a poor ionic conductor) will not furnish any protection. This effectively stops the oxidation reactions on the metal surface by transferring them to the galvanic anode, which will be sacrificed in favour of the structure under protection. Prevention of corrosion by cathodic protection (CP) works by introducing another metal (the galvanic anode) with a much more anodic surface, so that all the current will flow from the introduced anode and the metal to be protected becomes cathodic in comparison to the anode. This is rather a simplified view of the corrosion process, because it can occur in several different forms. As a result, in ferrous metals, a general covering of rust is formed over the whole surface, which will eventually consume all the metal. (The flow of electrons is in the opposite direction of the flow of electric current.)Īs the metal continues to corrode, the local potentials on the surface of the metal will change and the anodic and cathodic areas will change and move. Conversely, as electrons flow from the electrolyte to the cathodic areas, the rate of corrosion is reduced. Electrons flow from the anodic areas into the electrolyte as the metal corrodes. As corrosion takes place, oxidation and reduction reactions occur and electrochemical cells are formed on the surface of the metal so that some areas will become anodic (oxidation) and some cathodic (reduction).
